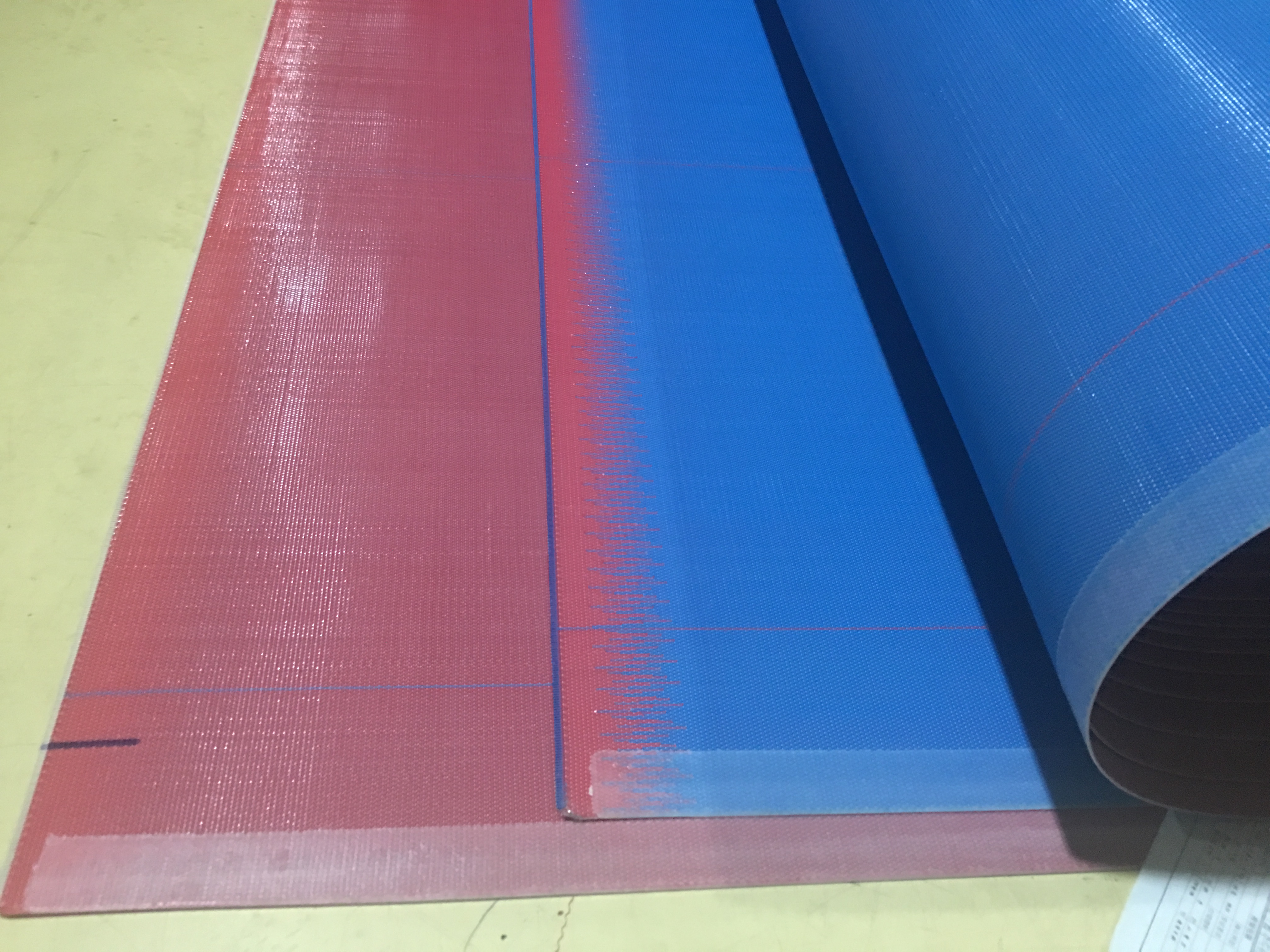
Analysis of the edge wear of the paper forming fabric:
First: The most severe wear of most paper machine is at the vacuum and non-vacuum joints (10-15cm from the edge of the screen, the solution: 1. Try to enlarge the width of the opening of the vacuum box. 2. Add normal pressure lubricating water to the edge of the vacuum box. 3. Add stiffeners at appropriate positions. 4. Check whether the edge wiper and the vacuum box have corners or gaps. Especially the joints of ceramic panels are weak links 5. Check whether the edges of the rollers are severely worn (the diameter becomes smaller after wear, so that the tension of the mesh is smaller than the normal mesh surface to further accelerate the wear) Second: The overall situation of excessive wear and tear: 1. The panel quality is not good enough. 2. The net tension is too small, the return tension of single-layer net is 3-4kg/cm, and the return tension of two-layer net is 5-6kg/cm. 3. Poor packing quality. 4. The net has a large air permeability and there is a lot of filler loss, and there are too many filler particles between the net and the vacuum box panel, which will cause the overall wear of the net to be faster. 5. The net air permeability is small and the water filtration is slow, but the vacuum degree increases and the wear is accelerated. 6. The speed of the guide Roller is not synchronized with the wire speed. 7. The network speed of the upper and lower network is not synchronized. Third: Local longitudinal wear and rapid wear: Whether there are stubbles, unevenness and gaps in the forming plate, wiper board, and vacuum box panel; whether the rollers are locally worn and rusted. Fourth: Partially longitudinally long drum: Whether there are stubbles or unevenness on the forming plate, wiper board, and vacuum box panel, whether the breast roller vacuum roller has protrusions such as solder joints, and whether the Rubber Roller has impurities. Fifth: Winding of the guide roller: The cleaning water pressure is low and there are many fibers inside the net; the air permeability of the net is low; there is a problem with the cleaning method. 15-20cm. Sixth: Vacuum box top slurry: the air permeability of the mesh is inappropriate, the slurry fiber is short and the loss is large, the quality of the retention aid is not good or the addition amount is small. Seventh: Large fluctuation range when the network is running: the corrector is not working properly, and the cutting edge of the network is not straight. Eighth: The net becomes narrow after a period of use: local wear of the forming plate, wiper board, vacuum box panel or guide roller causes the marking line of the net to run for a period of time to become slanted (partial net operation is inconsistent).